ITAMCO's Joel Neidig to speak at Fabtech 2023
ITAMCO at Fabtech 2023
We’re thrilled to announce that Joel Neidig will be speaking at Fabtech this year!
Fabtech is North America’s largest metal forming, fabricating, welding, and finishing event. The manufacturing event will feature more than 1,500+ world-class suppliers.
You can find out more about Fabtech here
Join us at the SME Zone in Booth B18000 at 1:00 p.m. to hear Joel discuss the exciting world of Additive Manufacturing!
Want to read more about Additive Manufacturing?
Making CNC Grinding More Energy Efficient
In 2020, the Clean Energy Smart Manufacturing Innovation Institute (CESMII) announced more than $6 million in funding for eight projects to improve energy-intensive manufacturing processes and to strengthen the U.S. manufacturing sector.
ITAMCO, West Virginia University, and Clemson University were chosen to develop hybrid modeling for energy efficient grinding processes for gear manufacturing.
PROBLEM TO BE SOLVED:
Grinding is of the upmost importance in industry, and is essential for creating parts from hard and brittle materials. However, out of all machining processes, it is the one with the highest energy consumption. (SEC) The total grinding time for ITAMCO’s Ring Gear (Pictured below) accumulates 11 hours of energy, and is responsible for 33% of the total manufacturing cost of the gear.
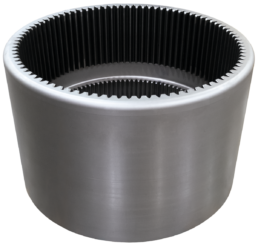
PROJECT OBJECTIVE:
The principal goal is to reduce the extremely high energy consumption of grinding processes for gear manufacturing by at least 15% through hybrid modeling of the grinding system holistically.
TECHNICAL APPROACH:
To achieve this goal, we will develop novel hybrid modeling methods that combine multi-physics equation-based models with data-driven machine learning models. The hybrid model input includes both machine tool parameters and sensor data as well as data from ERP and tool management systems. The hybrid model’s output provides grinding process parameters (wheel speed, depth of cut, infeed duration) as well as grinding tool reconditioning schedule and parameters (dressing and sharpening) that reduce the overall grinding system’s SEC. The model will be prototypically implemented in the industrial testbed will be located on-premise at ITAMCO, a leading US gear manufacturer and SME.
POTENTIAL IMPACT:
The US demand for gears is expected to grow by 6.4% to $40 billion in sales. Grinding will remain the core technology to produce large-scale, high-quality gear components. The novel, scalable, and generalizable hybrid modeling approach and its deployment in the CESMII SM platform environment will provide a blueprint for other use cases to reduce the energy consumption of the US grinding industry.
ITAMCO’s Niles ZP40, which is the primary machine on which their Ring Gear is ground.
BENEFITS TO CESMII:
The project showcases rapid recovery of Smart Manufacturing adoption cost through energy savings and productivity increases in an industry with energy intensive processes. The project creates an opportunity to scale its impact for other interested CESMII members across industries (automotive, aerospace, medical, etc.) and applications (milling, turning, etc.) within the larger CESMII network.
IMPACT VS PERFORMANCE METRICS:
15% reduction in energy consumption & 3-7% increase in productivity lead to an estimated increased throughput of 28 additional units, and annual savings of ~$143,000 and ~1,000t CO2at ITAMCO alone.
Information from Dr. Thorsten Wuest, West Virginia University
ITAMCO Wins Small and Medium-sized Manufacturer of the Year
In an annual event to commemorate innovation in hardtech and manufacturing, ITAMCO has won the small and medium-sized manufacturer of the year award!
From the Fourth Revolution Website: “Founded in 1955, ITAMCO is entering the era of employing the 4th generation and currently employees 124 employees. ITAMCO manufacturers gears that are supplied to the oil and gas industry and is starting to support the EV industry as well.”
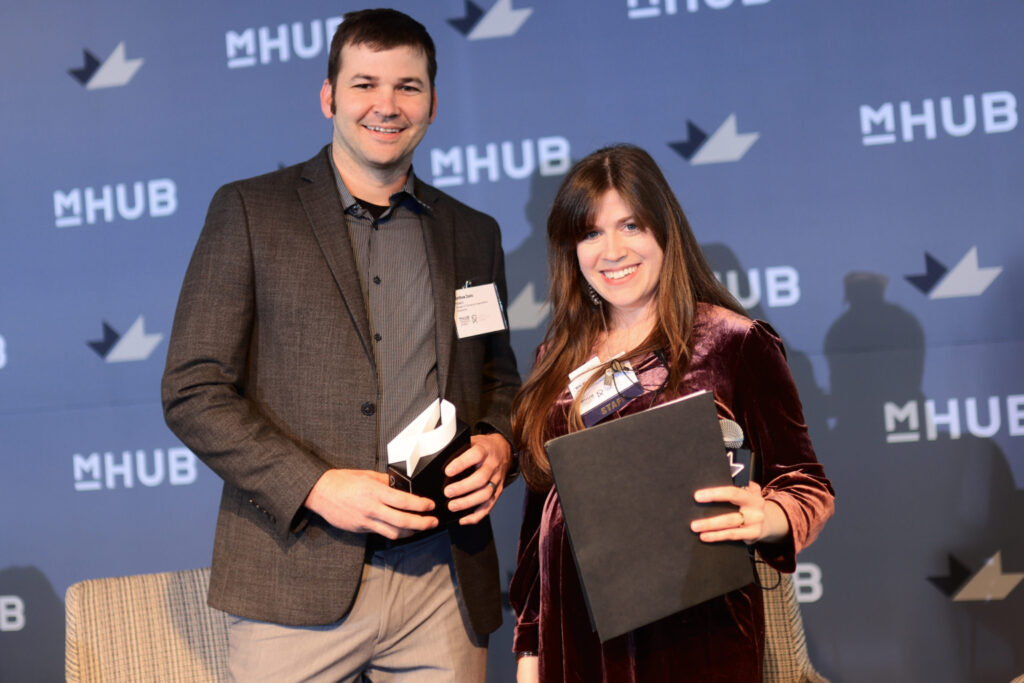
The Fourth Revolution would also go on to congratulate the winners: “Congratulations again to the award winners, and to all the award finalists and nominees. Together, we will ensure that the region’s manufacturing sector is driven, infused with world-class talent, and continues its reign as a global leader into the future.”
For more information, view the original article here.
SEE WHAT ITAMCO HAS BEEN DOING IN THE EV INDUSTRY
Grant to Improve DoD Smart Tech
The Indiana Economic Development Corporation (IEDC) is awarding grants totaling $650,000 to three Hoosier companies to spur technology development in the defense industry. The grant recipients include Indiana Technology and Manufacturing Companies (ITAMCO), J&L Dimensional, and Mursix Corporation.
IEDC says these businesses will create new smart technology platforms with the goal of improving data management, efficiency, and analysis among contractors with the Department of Defense.
Details of the grants are below:
- ITAMCO, Marshall County – $150,000 to develop a machine learning, smart-data-analysis platform for manufacturers that provides real-time adjustment and optimization utilizing artificial intelligence for product quality monitoring. The project will enhance efficiencies and lower costs for manufacturers. The project is being supported by Rolls-Royce and SIMBA Chain.
- J&L Dimensional, LaPorte County – $250,000 to create a platform that improves decision making, increases efficiency of production and maintenance, repair and overhaul operations, and lowers costs by creating linkages to previously inaccessible data. The project is being supported by Rolls-Royce & Purdue University
- Mursix Corp., Delaware County – $250,000 to utilize data to enhance the properties of the company’s digital thread capabilities for future commercial automotive, medical and military applications. The project is being supported by Columbus-based Cummins Inc., Terre Haute-based ICTT System Sciences, Indianapolis-based IntelAdvise and Purdue Polytechnic.
“As a state, we’re committed to fueling innovation and investing in disruptive technologies like digital thread to cultivate a 21st century defense ecosystem,” said retired Major General Omer Tooley Jr., the IEDC’s president of defense development. “These grants will allow Indiana companies to continue innovating, competing and developing new solutions that encourage long-term, sustainable growth in Indiana’s defense industry. We’re excited to collaborate with the Air Force Research Laboratory to enhance the technical capabilities of our nation’s supply chain and look forward to supporting these projects from start to finish.”
The grants, approved through the state’s 21st Century Research & Technology Fund, will propel investments already being made by the companies and their support organizations.
ITAMCO Developing Portable Runway Mat
ITAMCO is competing for a Phase II Small Business Innovation Research (SBIR) grant for additive manufactured portable runway mat which could be used by the United States military all over the globe. The current AM2 matting being used for portable airfields dates back to the Vietnam era. The updated matting must be easy to install and store yet withstand multiple take-offs and landings of aircraft
ITAMCO, working with Professor Pablo Zavattieri in the Lyles School of Civil Engineering at Purdue University, is developing the next-generation material called phase-transforming cellular materials, or PXCMs, for the US Air Force. The design can be scaled to almost any size and can only be produced by 3D printing.
The company won Phase 1 SBIR funding, earning it the right to compete for the Phase II. ITAMCO is now in the prototype and testing stage. The durable matting can restore itself to its original contour and would allow for planes to land on the temporary runway 30 minutes after it’s laid in place and tested. Continuing research will allow it to develop a robust sheet or roll of the matting.
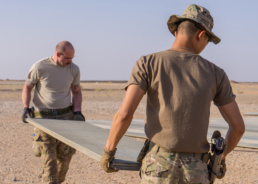
Tech. Sgt. Dan Zimmerman (back) and Senior Airman Thet Tun (front) carry a piece of AM2 matting material, Camp Dwyer, Afghanistan, July, 12, 2016. Zimmerman and Tun constructed a 100’ x 100’ helicopter landing zone out of AM2 matting to support the medical facility at Camp Dwyer. (Courtesy photo by 451 Air Expeditionary Support Squadron)
Additive Manufacturing Virtual Summit
ITAMCO is excited to announce the third-annual Additive Manufacturing Summit on Tuesday, July 14 from 1-4 p.m. EST.
This year’s event will be held virtually and focus on educating and informing attendees about the growing industry surrounding Additive Manufacturing (AM). AM has seen incredible growth and the future for the technology is bright. Register now to hear speakers from leading companies in the AM space.
Speakers include:
- JANET KAR, CMO, Link3D
- ELIANA FU, Senior Engineer: Additive Technologies, Relativity Space
- ANDRE WEGNER, Founder and CEO, Authentise
- BRENT KEPHART, Global Portfolio Development Executive, Siemens
- ANJON ROY, Vice President of Market Development, SIMBA Chain
Changes in Smart Manufacturing
West Virginia University and ITAMCO are advancing smart manufacturing with a $901,486 grant awarded by the United States Department of Energy’s Clean Energy Smart Manufacturing Innovation Institute (CESMII). The project’s goal is to improve the energy efficiency of manufacturing across the United States.
Gears are a critical component industry. Thorsten Wuest, the J. Wayne and Kathy Richards Faculty Fellow and assistant professor of industrial and management systems engineering in the Benjamin M. Statler College of Engineering and Mineral Resources, believes the demand for gears in the United State alone will grow by 6.4 percent to $40 billion in sales.
Researchers from the University at Buffalo and Indiana Technology and Manufacturing Companies (ITAMCO) collaborative on this project and will develop a holistic hybrid model to predict the specific energy consumption of large-scale grinding processes.
The focal point of the project is a large-scale internal double wheel end gear that is approximately 3 feet in diameter with a processing time of over 11 hours. The gear is used in heavy mining and construction equipment.
“In manufacturing there is not much previous work available, especially not at the level we are proposing with direct industrial application through our industrial partner Indiana Technology and Manufacturing Companies (ITAMCO) and the reach of CESMII,” Wuest said.
Hybrid analytics, a relatively newer field, merges traditional, physics-based modeling with data-driven machine learning models. The proposed project will directly impact operations at ITAMCO and has the potential to reduce energy consumption by large-scale grinding by at least 15 percent.
Wuest explained that for CNC grinding systems energy accounts for about 33 percent of the overall manufacturing cost.
“Reducing the energy consumption by improving the grinding strategy based on hybrid modeling does not only reduce the environmental impact, but it also improves the company’s bottom line and further increases the competitiveness of U.S. manufactured high-tech goods on the global marketplace,” he continued.
According to Wuest, grinding has the highest rate of energy consumption of all machining processes, and this process isn’t going anywhere soon.
Leading Through Collaboration
Indiana Technology and Manufacturing Companies (ITAMCO) have long been recognized as premier advanced manufacturing and technology firms.
We collaborate with like-minded professionals from the world’s most respected companies, institutions, and universities to deliver technology, engineering, and manufacturing solutions. We are dedicated to solving complex challenges, streamlining businesses, and strengthening our customer’s bottom line.
Advancing Leadership in Smart Manufacturing
The Clean Energy Smart Manufacturing Innovation Institute (CESMII) announced more than $6 million in funding for eight projects to improve energy-intensive manufacturing processes and strengthen the U.S. manufacturing sector.
ITAMCO, West Virginia University, and the University of Buffalo will develop hybrid modeling for energy efficient grinding processes for gear manufacturing.
Read the entire press release below:
Today, the U.S. Department of Energy (DOE)’s Clean Energy Smart Manufacturing Innovation Institute (CESMII) announced more than $6 million for eight projects to improve energy-intensive manufacturing processes and strengthen the U.S. manufacturing sector.
CESMII is a part of Manufacturing USA, a network of regional institutes that have a specialized technology focus to increase U.S. manufacturing competitiveness and promote a robust and sustainable national manufacturing research and development (R&D) infrastructure. CESMII works with American companies to spur innovations in new, integrated, systematic “smart” manufacturing processes with a highly skilled manufacturing workforce and a vibrant supply chain.
The Trump Administration has identified advanced manufacturing as one of the vital industries of the future. The White House Office of Science and Technology Policy’s Oct. 2018 “Strategy for American Leadership in Advanced Manufacturing” calls for new smart manufacturing technologies to “facilitate a digital transformation in the manufacturing sector by enabling the application of big data analytics and advanced sensing and control technologies to a host of manufacturing activities.”
“Advances in digital technologies and other forms of ‘smart manufacturing’ can improve the efficiency and competitiveness of America’s manufacturing sector,” said Alex Fitzsimmons, Deputy Assistant Secretary for Energy Efficiency. “In partnership with industry, universities, and the National Laboratories, DOE’s investments will help position the U.S. for global leadership in the advanced manufacturing industries of the future.”
The following projects are selected for negotiations:
- Auburn University and Rayonier Advanced Materials will develop a soft sensor and predictive control for anti-foaming agent usage, wash water flow, and pulp quality in paper manufacturing using statistics pattern analysis and machine learning.
- Baxter Solutions and Purdue University will develop real-time, non-invasive, process monitoring system for pharmaceutical lyophilization (also known as freeze-drying) equipment based on a wireless network of vacuum and temperature sensors.
- Honeywell, Virginia Tech, Bodycote, and Seco-Warwick will develop new sensors, monitoring and data analytic methods and apply them to three industrially relevant thermal processes.
- Pennsylvania State University, Texas A&M University (TAMU), and University of Texas Rio Grande Valley (UTRGV) will develop novel self-powered sensors and identify actuators needed to collect information and respond to actions for machines including legacy machines for key applications.
- Rensselaer Polytechnic Institute and IBM will develop a modeling engine with sophisticated predictive capabilities to model a variety of manufacturing processes and demonstrate the capabilities on a critical complementary metal–oxide–semiconductor transistor manufacturing process.
- Rutgers, The State University of New Jersey, and Janssen Pharmaceuticals will develop advanced process models, sensors and data integration architecture that will be demonstrated on wet granulation, drying and milling in pharmaceutical manufacturing processes.
- UTRC, Purdue University, and the Connecticut Center for Advanced Technology Inc. will develop a simulation and testing framework to determine the feasibility of using ultrasound to mitigate dirty white spot defects in forged IN 718 turbine parts in the Vacuum Arc Remelting process.
- West Virginia University, University of Buffalo, and Indiana Technology and Manufacturing Companies (ITAMCO) will develop and test hybrid modeling for energy efficient grinding processes for gear manufacturing in collaboration with the industrial partners.
Founded in 2016, in partnership with DOE’s CESMII is the third institute funded by EERE’s . CESMII accelerates smart manufacturing adoption through the integration of advanced sensors, data analytics, platforms and controls to improve productivity, precision, performance, and energy consumption in manufacturing.
To create and sustain American leadership in advanced manufacturing, DOE is investing in new industrial technologies, materials, and processes to help bolster American manufacturing. Last month, EERE’s Advanced Manufacturing Office announced $187 million in new investments for high-impact manufacturing technologies, materials, and processes to strengthen the domestic manufacturing base.
Employee Highlight – Kurt Hanby
ITAMCO would like to highlight some of our valuable employees. Meet Kurt!
Kurt Hanby works in our business development department. We asked him a few questions, and we thought we’d share his answers with you.
1. How long have you worked at ITAMCO?
6.5 years
2. What's the best thing about your job?
Building relationships with people.
3. What is your job at ITAMCO?
Sales and Customer Service
4. What is your favorite part about ITAMCO?
The people. Working alongside friends, mentors, and people that care about you.
5. What's something most people don't know about you?
I like to cook.
6. Where's your favorite place in the world?
Trossachs National Park, Scotland
7. What do you like to do when you're not at work?
Hunt, fish, and camp
8. If you could pick one superpower, what would it be?
To be in two places at once.
9. If you could meet anyone, dead or alive, who would it be and why?
The Apostle Paul. To hear more about his life.
10. Coffee or Tea?
Strong coffee for sure!
Thank you Kurt! We will continue to bring you other employee spotlights throughout the year.
USS Gerald R Ford at-sea Testing
The USS Gerald R Ford (CVN 78) is in the middle of at-sea testing of her Electromagnetic Aircraft Launch System (EMALS) and Advanced Arresting Gear (AAG) technology.
The Aresting gear is a mechanical system used to rapidly decelerate an aircraft as it lands on an aircraft carrier. The new AAG system, introduced in this new class of carriers, is the replacement for older hydraulic arresting gear. The more advanced system offers finer control, less maintenance, and expands capabilities to a broader range of aircraft, including UAVs. ITAMCO manufactures a critical component used in the AAG.
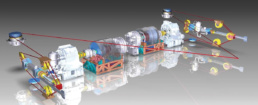
Advanced Arresting Gear for US Navy Gerald R. Ford-class aircraft carriers
See the system in action Below:
Guide to Additive Manufacturing
We've already done our homework on Additive Manufacturing. Want our notes?
Additive Manufacturing is changing the way manufacturing gets done, but what is it? How does it work? What are the benefits and limitations? What industries are benefiting the most? ITAMCO answers these questions and examines how 3D printing compares to traditional manufacturing.
Check out what else ITAMCO has been doing in the Additive Manufacturing world!
Tracking Production with QuPiD
A decade ago ITAMCO was searching for a way to more efficiently monitor the production process.
How long did it take to manufacture one part? How long did each process take? Were were problems occurring? We needed a way to track these things and make production as productive and efficient as possible. Our in-house developers began creating QuPiD as a way to better track the way we manufacture.
The software is always being being updated and expanded. QuPiD now works as follows:
- Each ITAMCO employee installs QuPiD on their mobile device
- They sign into a job via QuPiD when they receive a part
- When they complete their operation of the Manufacturing Order (MO), they sign out of that job.
- The part continues to the next stage.
Data submitted cannot be deleted, altered, or edited, and it can always be traced back to the original transaction author. QuPiD can now immutably verify every transaction that is uploaded. This also plays a role in helping ITAMCO to adhere to the ISO9001:2015 standard.
ITAMCO Renews ISO 9001:2015 Certification
ITAMCO is proud to announce that we have renewed our ISO 9001:2015 Certification.
ISO 9001 is the most widely recognized quality management standard and helps organizations to meet the expectations and needs of their customers. ITAMCO engaged in a rigorous audit of our business processes as well as our quality environments during the ISO 9001:2015 recertification process. You can click here to see a copy of our certification.
Thank you to the entire ITAMCO team for all of your hard work and commitment to excellence.
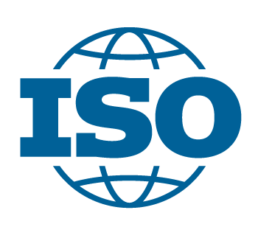
Siemens Expands Additive Manufacturing Portfolio Through Acquisition of Atlas 3D
PLANO, Texas, Nov. 12, 2019 /PRNewswire/ — Siemens announced today that it has signed an agreement to acquire Atlas 3D, Inc., a Plymouth, Indiana-based developer of software that works with direct metal laser sintering (DMLS) printers to automatically provide design engineers with the optimal print orientation and requisite support structures for additive parts in near real-time. Atlas 3D will join Siemens Digital Industries Software, where its solutions will expand additive manufacturing capabilities in the Xcelerator portfolio of software.
Sunata™ software uses thermal distortion analysis to provide a simple, automated way to optimize part build orientation and generate support structures. This approach allows the designer—rather than the analyst—to perform these simulations, thereby reducing the downstream analysis that needs to be conducted via Simcenter™ software to achieve a part that meets design requirements. Siemens plans to make the Atlas 3D solution available through its online Additive Manufacturing Network.
“We welcome Atlas 3D to the Siemens community as the newest member of our additive manufacturing team. Our solutions industrialize additive manufacturing for large enterprises, 3D printing service bureaus, design firms and CAD designers,” said Zvi Feuer, Senior Vice President, Manufacturing Engineering Software of Siemens Digital Industries Software. “The cloud-based Sunata software makes it easy for designers to determine the optimal way to 3D print parts for high quality and repeatability. The combination of Sunata with the robust CAE additive manufacturing tools in Simcenter enables a ‘right first time’ approach for industrial 3D printing.”
“Siemens is a leader in additive manufacturing, with the most integrated and functionally robust solutions in the industry, so we are excited to join the team,” said Chad Barden, Chief Executive Officer of Atlas 3D. “The power of Sunata is that it equips designers to more easily design parts that are printable, which helps companies more quickly realize the benefits of additive manufacturing. As part of Siemens, we look forward to introducing Sunata to customers who already have Siemens’ AM solutions and can achieve new efficiencies in their front-end design-for-additive process, as well as companies who have yet to start their additive manufacturing journey.”
The high rate of 3D print failures is a key challenge companies face in leveraging additive manufacturing for high-volume production. Parts often need to go through several design and analysis iterations before the optimal build orientation and support structures are determined. Typically, designers don’t have the capabilities to consider such factors as part orientation, distortion, and heat extraction uniformity in their design. This puts the onus on engineering specialists to resolve such issues.
Atlas 3D’s Sunata software solves this problem by giving front-end designers a quick, easy and automated way to get much closer to a “right first time” build. Sunata is a GPU-accelerated high-performance computing additive manufacturing software solution that can deliver results up to one hundred times faster than other build simulation solutions on the market. GPU-accelerated computing is the employment of a graphics processing unit (GPU) along with a computer processing unit (CPU) to facilitate processing-intensive operations such as deep learning, analytics and engineering applications.
The acquisition is due to close in November 2019. Terms of the transaction were not disclosed.
Siemens Digital Industries Software is driving transformation to enable a digital enterprise where engineering, manufacturing and electronics design meet tomorrow. The Xcelerator portfolio helps companies of all sizes create and leverage digital twins that provide organizations with new insights, opportunities and levels of automation to drive innovation. For more information on Siemens Digital Industries Software products and services, visit www.sw.siemens.com or follow us on LinkedIn, Twitter, Facebook and Instagram. Siemens Digital Industries Software – Where today meets tomorrow.
Siemens Digital Industries (DI) is an innovation leader in automation and digitalization. Closely collaborating with partners and customers, DI drives the digital transformation in the process and discrete industries. With its Digital Enterprise portfolio, DI provides companies of all sizes with an end-to-end set of products, solutions and services to integrate and digitalize the entire value chain. Optimized for the specific needs of each industry, DI’s unique portfolio supports customers to achieve greater productivity and flexibility. DI is constantly adding innovations to its portfolio to integrate cutting-edge future technologies. Siemens Digital Industries has its global headquarters in Nuremberg, Germany, and has around 76,000 employees internationally.
Siemens AG (Berlin and Munich) is a global technology powerhouse that has stood for engineering excellence, innovation, quality, reliability and internationality for more than 170 years. The company is active around the globe, focusing on the areas of power generation and distribution, intelligent infrastructure for buildings and distributed energy systems, and automation and digitalization in the process and manufacturing industries. Through the separately managed company Siemens Mobility, a leading supplier of smart mobility solutions for rail and road transport, Siemens is shaping the world market for passenger and freight services. Due to its majority stakes in the publicly listed companies Siemens Healthineers AG and Siemens Gamesa Renewable Energy, Siemens is also a world-leading supplier of medical technology and digital healthcare services as well as environmentally friendly solutions for onshore and offshore wind power generation. In fiscal 2019, which ended on September 30, 2019, Siemens generated revenue of €86.8 billion and net income of €5.6 billion. At the end of September 2019, the company had around 385,000 employees worldwide. Further information is available on the Internet at www.siemens.com.
Note: A list of relevant Siemens trademarks can be found here. Other trademarks belong to their respective owners.
SOURCE Siemens PLM
Related Links
http://www.siemens.com