West Virginia University and ITAMCO are advancing smart manufacturing with a $901,486 grant awarded by the United States Department of Energy’s Clean Energy Smart Manufacturing Innovation Institute (CESMII). The project’s goal is to improve the energy efficiency of manufacturing across the United States.
Gears are a critical component industry. Thorsten Wuest, the J. Wayne and Kathy Richards Faculty Fellow and assistant professor of industrial and management systems engineering in the Benjamin M. Statler College of Engineering and Mineral Resources, believes the demand for gears in the United State alone will grow by 6.4 percent to $40 billion in sales.
Researchers from the University at Buffalo and Indiana Technology and Manufacturing Companies (ITAMCO) collaborative on this project and will develop a holistic hybrid model to predict the specific energy consumption of large-scale grinding processes.
The focal point of the project is a large-scale internal double wheel end gear that is approximately 3 feet in diameter with a processing time of over 11 hours. The gear is used in heavy mining and construction equipment.
“In manufacturing there is not much previous work available, especially not at the level we are proposing with direct industrial application through our industrial partner Indiana Technology and Manufacturing Companies (ITAMCO) and the reach of CESMII,” Wuest said.
Hybrid analytics, a relatively newer field, merges traditional, physics-based modeling with data-driven machine learning models. The proposed project will directly impact operations at ITAMCO and has the potential to reduce energy consumption by large-scale grinding by at least 15 percent.
Wuest explained that for CNC grinding systems energy accounts for about 33 percent of the overall manufacturing cost.
“Reducing the energy consumption by improving the grinding strategy based on hybrid modeling does not only reduce the environmental impact, but it also improves the company’s bottom line and further increases the competitiveness of U.S. manufactured high-tech goods on the global marketplace,” he continued.
According to Wuest, grinding has the highest rate of energy consumption of all machining processes, and this process isn’t going anywhere soon.
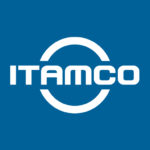
ITAMCO
ITAMCO has been recognized as one of the premier advanced manufacturing and technology firms in the United States. We collaborates with like-minded professionals from the world’s most respected companies and universities across the globe to solve complex challenges and deliver innovative solutions.