ITAMCO Invests in Employees and NUM CNC Technology
ITAMCO, a leader in precision gear and spline manufacturing, is once again demonstrating its commitment to both technological advancement and employee development through a renewal project for a Fellows 36-6 gear shaping machine. Partnering with NUM, a global leader in CNC automation, ITAMCO has integrated NUM’s Flexium+ CNC control and software into a legacy machine now primed for increased productivity and longevity.
This initiative highlights ITAMCO’s dedication to providing its workforce with opportunities to grow and master the latest technologies. By involving employees in the retrofitting process, ITAMCO fosters a culture of learning and innovation. This hands-on experience allowed team members to gain valuable skills and knowledge in advanced manufacturing technology, ensuring the company remains at the forefront of the industry.
“ITAMCO clearly believes in empowering their employees with the tools and knowledge to excel,” comments Tom Vascik from NUM US. “Projects like the Fellows 36-6 shaper retrofit not only enhance their production capabilities, but also provide invaluable training opportunities for their in-house software development and integration teams. This investment in their personnel, coupled with NUM’s collaborative engineering approach have led to a capable machine and personnel with direct practical knowledge of the software application and hardware.”
Investing in People: A Cornerstone of ITAMCO's Success
ITAMCO has a long-standing history of investing in its employees. This commitment is evident in various initiatives:
- Employee Ownership: ITAMCO transitioned to a 100% employee-owned company in October 2024, demonstrating a strong belief in shared success and empowering employees with ownership in the company.
- Continuous Learning: ITAMCO actively promotes a culture of learning by providing resources and opportunities for employees to enhance their skills and knowledge. This includes internal training programs, partnerships with educational institutions, and encouraging participation in industry events.
- Advanced Technology Adoption: By embracing cutting-edge technologies like NUM's Flexium+ CNC and shaping conversational, ITAMCO ensures its operators are equipped to work with the latest advancements in the field.
Central to the update is the integration of NUM’s Flexium+ CNC platform, a comprehensive solution encompassing CNC hardware, servo drives, and motors, along with NUM’s intuitive gear shaping conversational programming software.
As Joel Neidig, Co-CEO at ITAMCO, points out, “Upgrading our gear shaper with NUM’s Flexium+ CNC control has been a transformative step for ITAMCO. The enhanced precision, faster cycle times, and intuitive programming capabilities are helping us produce quality gears more efficiently. We’re excited about the new possibilities this brings to our team and our customers.”
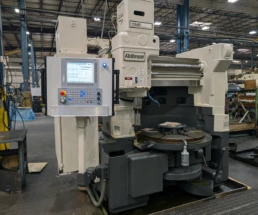
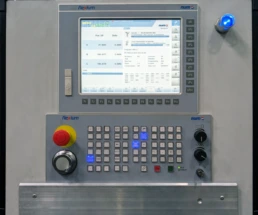
About NUM
NUM is a leading global provider of CNC automation solutions. The company’s innovative products and services enable manufacturers to achieve greater efficiency, productivity, and quality in their operations. NUM has a proven track record of delivering cutting-edge solutions to a wide range of industries, including aerospace, automotive, medical, and energy.
Joel and Mark Neidig Honored With ACG Indiana Small Cap Value Award
Joel and Mark Neidig, Co-Chief Executive Officers of ITAMCO (Indiana Technology and Manufacturing Companies), have been honored with the ACG Indiana Annual Small Cap Value Award – a prestigious accolade that recognizes the company’s exceptional leadership, innovation, and enduring impact on the manufacturing and technology landscape. The award, one of the most competitive distinctions in the region, was the result of a unanimous vote by the ACG Indiana selection committee.
The Association for Corporate Growth (ACG) is a global organization focused on driving middle-market growth. Its Indiana chapter annually celebrates top-performing companies that embody strategic excellence, value creation, and leadership integrity. The Small Cap Value Award spotlights organizations that consistently deliver exceptional results while embodying the entrepreneurial spirit.
“This award means so much because it reflects the dedication of every employee-owner at ITAMCO,” said Joel Neidig. “Being a 100% Employee-Owned Company through our ESOP (Employee Stock Ownership Plan) is core to who we are. Every person here has a stake in our success, and that shared ownership drives a culture of accountability, innovation, and pride.”
Founded in 1955, ITAMCO has transformed from a precision gear manufacturer into a national leader in advanced manufacturing and digital technology integration. Today, it uniquely blends legacy craftsmanship with future-facing innovation, incorporating additive manufacturing, blockchain, Industrial IoT, and smart factory solutions.
The company’s 100% ESOP ownership structure plays a central role in its success. As a fully employee-owned company, ITAMCO fosters a culture where every team member is empowered and invested. This shared sense of purpose not only enhances performance and customer satisfaction but also strengthens long-term strategic thinking.
“The ESOP is more than a financial structure – it’s a cultural foundation,” added Mark Neidig. “It encourages a deep sense of ownership at every level of our company, and that collective mindset is what fuels our drive to lead, adapt, and grow. This is why our incredible team has earned this award.”
The ACG Indiana committee cited ITAMCO’s unique employee ownership model, rapid innovation adoption, and unwavering leadership as decisive factors in its unanimous selection.
With its eyes on the future and a foundation rooted in shared ownership and values, ITAMCO continues to redefine what it means to be a next-generation American manufacturer.
About ACG Indiana
The Association for Corporate Growth (ACG) is the premier global community for middle-market M&A deal-makers and business leaders focused on driving growth. ACG Indiana's annual awards honor the state's most distinguished companies for outstanding performance, innovation, and leadership.
ITAMCO Announces New Co-CEOs
ITAMCO, a global leader in gear manufacturing and advanced manufacturing technology, proudly announces the appointment of Mark Neidig and Joel Neidig as co-CEOs, marking a significant transition from second-generation family leadership to the third generation. This strategic move positions the company for continued growth and innovation as it embraces new challenges in the evolving manufacturing landscape.
With a legacy spanning over six decades, ITAMCO has established itself as a pioneer in gear manufacturing, providing high-quality products and cutting-edge manufacturing solutions to clients worldwide. The Neidig family’s commitment to excellence and innovation has been the cornerstone of ITAMCO’s success, and the appointment of Mark and Joel Neidig underscores the company’s dedication to fostering a future of leadership driven by experience and expertise.
Mark Neidig brings a wealth of knowledge in manufacturing and operations, having dedicated more than 20 years to ITAMCO. His extensive background in optimizing production processes and driving operational efficiency has been instrumental in enhancing the company’s capabilities and meeting the diverse needs of its customers. Mark’s hands-on leadership approach and deep understanding of the manufacturing sector position ITAMCO for continued operational excellence.
Joel Neidig, with his experience in multiple startups and a proven track record as a CEO, complements Mark’s operational expertise with his insights into financial and technology development. Over the years, Joel has cultivated a keen understanding of the intersection between technology and manufacturing, ensuring that ITAMCO remains at the forefront of industry advancements. His strategic vision and innovative mindset are poised to propel the company into new markets and opportunities.
“We are excited to enter this new chapter in ITAMCO’s history,” said Mark Neidig. “As co-CEOs, Joel and I are committed to honoring the legacy built by our family while embracing innovative practices that will ensure our continued success in a competitive global market.”
Joel Neidig added, “Together, we will leverage our combined experience to drive ITAMCO forward. We are dedicated to investing in our people, technology, and processes, ensuring that we not only meet but exceed our customers’ expectations.”
As ITAMCO embarks on this new era of leadership, the company remains focused on its mission to provide exceptional manufacturing solutions and gear products to clients around the globe. The Neidig cousins are poised to build on the strong foundation laid by their predecessors, fostering a culture of innovation and excellence that has defined ITAMCO for generations.
ITAMCO Becomes 100 Percent Employee-Owned
ITAMCO is pleased to announce that it has become a 100% employee-owned company through the creation of a new ESOP (Employee Stock Ownership Plan). “We’re excited to become a 100% employee-owned business,” said Gary Neidig, President of ITAMCO.
ITAMCO, an advanced manufacturing and technology firm, collaborates with companies around the globe to deliver innovative solutions. “We are proud of what makes ITAMCO unique, and employee ownership is the next step in our journey of continual improvement. We treat each of our clients like true partners throughout the business relationship process and now all of our employees will be true partners in our business as owners,” added Gary Neidig.
Employee ownership complements ITAMCO’s philosophy of always searching for best practices and innovative solutions. “Our transition to a 100% employee-owned company is a natural extension of what enabled us to become a strong, cutting-edge company. It embodies our core values of creating a culture of learning, a place to create, collaborate with others, and doing what needs to be done to get the right solution. Our ESOP is the best investment we can make in each other, our clients, suppliers and for the successful future of our business,” said Neidig.
Through ITAMCO’s ESOP plan, employees will earn shares in the business while working for the Company. The ESOP benefit is funded entirely by Company contributions and requires no out-of-pocket investment by employees. Employee ownership ensures ITAMCO’s continued ability to serve clients as an independent enterprise while sharing in the Company’s long-term growth and success.
Neidig goes on to state, “With the best interests of our stakeholders in mind, becoming a 100% employee-owned business secures the Company’s future for all. With this approach, we keep operating with existing leadership without missing a beat. We’ll maintain everything that’s great about ITAMCO and transition to employee ownership smoothly. We believe our employee-owned culture and benefits will help us retain our talented employees, recruit new talent, and continue to provide exceptional services across the country and throughout the world. Our ESOP is the perfect embodiment of our company culture where we work as a team. Our company stands here today because of employees’ efforts day in and day out and I’m thankful for each one of our new employee owners who made this transition possible. ITAMCO’s goal is to be a partner for its clients, not just a manufacturer. Now as an employee-owned company, that goal is truer than ever before.”
Direct Lithium Extraction Technology
ITAMCO's Strategic Move into a the Thriving DLE Market
In the rapidly evolving landscape of energy and resource extraction, the quest for efficient, sustainable methods to harvest critical minerals has led to the rise of Direct Lithium Extraction (DLE) technology. This cutting-edge approach promises to revolutionize the lithium industry by streamlining extraction processes, reducing environmental impact, and meeting the soaring global demand for lithium-ion batteries. Among the pioneers in this promising field stands ITAMCO (Indiana Technology and Manufacturing Companies), a company with a track record in innovation and expertise, particularly drawn from its experience in hydraulic fracturing within the oil industry.
The Rise of Direct Lithium Extraction
Lithium, a key component in the production of batteries for electric vehicles (EVs), renewable energy storage, and portable electronics, has seen a surge in demand. Traditional lithium extraction methods, such as solar evaporation ponds and mineral extraction, pose significant environmental challenges and are often slow and inefficient. In contrast, DLE technologies offer a more sustainable and economically viable solution.
DLE techniques involve extracting lithium directly from brines or geothermal waters using selective sorbents, membranes, or other technologies. These methods not only enhance extraction efficiency but also minimize the environmental footprint by reducing water consumption and avoiding ecosystem disruption.
ITAMCO's Experience in Hydraulic Fracturing
ITAMCO’s foray into DLE technology draws intriguing parallels with its experience in hydraulic fracturing (fracking) for oil extraction. Historically, ITAMCO has been involved in developing and deploying advanced technologies in the oil and gas sector, including sophisticated hydraulic fracturing techniques. This experience has endowed ITAMCO with valuable insights into geology, fluid dynamics, and the logistical challenges of resource extraction from complex environments.
Leveraging Expertise for DLE Advancement
The transition from hydraulic fracking to DLE is not just a shift in focus but a strategic evolution. ITAMCO’s proficiency in handling complex fluid systems, optimizing well designs, and managing large-scale operations translates seamlessly into the realm of DLE. Both industries share commonalities in operational challenges, technological innovation, and the need for sustainable practices.
Capitalizing on Market Opportunities
ITAMCO’s move into DLE positions the company at the forefront of an expanding market with enormous potential. As global demand for lithium continues to escalate, efficient and environmentally responsible extraction methods will be paramount. ITAMCO’s experience and technological prowess uniquely position it to innovate and lead in this burgeoning sector.
Joel Neidig to Deliver Keynote Address at AI in Manufacturing Workshop Series
Joel Neidig, Director of R&D at ITAMCO, is set to deliver the keynote address at the upcoming AI in Manufacturing Workshop Series hosted by CESMII (the Clean Energy Smart Manufacturing Innovation Institute). The event, scheduled for May 14th, will bring together industry experts, researchers, and stakeholders to explore the transformative potential of artificial intelligence (AI) in manufacturing.
With over two decades of experience in the manufacturing sector, Joel Neidig is recognized for his pioneering work in leveraging AI, IoT, and Industry 4.0 technologies to drive operational efficiency and productivity. At ITAMCO, a leading provider of advanced manufacturing solutions, Neidig has spearheaded numerous initiatives aimed at harnessing the power of AI to optimize manufacturing processes, reduce costs, and enhance product quality.
In his keynote address, Neidig is expected to share insights into the role of AI in reshaping the future of manufacturing. He will discuss how AI-driven technologies such as machine learning, predictive analytics, and digital twins are revolutionizing traditional manufacturing practices, enabling companies to gain deeper insights, make data-driven decisions, and achieve new levels of competitiveness in the global marketplace.
One of the key themes Neidig is likely to address is the importance of collaboration and knowledge-sharing in advancing AI adoption in manufacturing. By fostering partnerships between industry, academia, and government agencies, Neidig believes that the manufacturing sector can accelerate the pace of innovation and unlock new opportunities for growth and sustainability.
Moreover, Neidig will highlight the critical role of workforce development in realizing the full potential of AI in manufacturing. As automation and AI technologies become increasingly integrated into manufacturing operations, there is a growing need for a skilled workforce capable of leveraging these technologies effectively. Neidig will underscore the importance of investing in education and training programs to equip the next generation of manufacturing professionals with the necessary skills and competencies.
In conclusion, Joel Neidig’s keynote address at the AI in Manufacturing Workshop Series promises to provide attendees with valuable insights into the transformative potential of AI in the manufacturing sector. By sharing his expertise and vision for the future of manufacturing, Neidig aims to inspire and empower industry stakeholders to embrace AI-driven technologies and drive innovation in the manufacturing industry.
Learn more and register for the event
Revolutionizing Potash Mining: ITAMCO's Advanced Gear Manufacturing Elevates Continuous Boring Miners
In the dynamic world of mining, efficiency and reliability are paramount, especially in industries like potash extraction where precision and durability are key. At the forefront of innovation in this sector is ITAMCO, a pioneer in advanced gear manufacturing. Today, we explore how ITAMCO’s cutting-edge gear technology is reshaping the landscape of potash mining, particularly in the realm of Continuous Boring Miner machines.
ITAMCO's Precision Gears: A Game-Changer for Continuous Boring Miners
Continuous Boring Miners play a vital role in potash mining operations, tirelessly excavating and transporting ore to the surface. The harsh and demanding conditions underground necessitate machinery that is not only robust but also precise in its movements. This is where ITAMCO’s advanced gear manufacturing capabilities come into play.
Key Benefits of ITAMCO's Gear Technology in Continuous Boring Miners:
- Enhanced Durability: Potash mining environments are known for their abrasive nature, putting considerable stress on mining equipment. ITAMCO’s gears are engineered with durability in mind, utilizing materials and coatings that withstand the rigors of continuous operation in challenging conditions.
- Precision Engineering: Continuous Boring Miners require precise control for efficient excavation. ITAMCO’s gears are manufactured with an emphasis on precision engineering, ensuring smooth and accurate movements critical for optimizing ore extraction.
- Customized Solutions: Recognizing the diversity of potash mining operations, ITAMCO collaborates closely with clients to provide tailored gear solutions. This customization ensures that gears are optimized for specific machine configurations, contributing to improved overall performance.
- Reliability: Unplanned downtime can have significant financial implications in the mining industry. ITAMCO’s commitment to reliability means that the gears in Continuous Boring Miners can be trusted to operate consistently, minimizing downtime and maximizing productivity.
Paving the Way for Efficient Potash Extraction
As the demand for potash continues to rise globally, mining operations face the challenge of meeting this demand while optimizing efficiency and minimizing environmental impact. ITAMCO’s advanced gear manufacturing capabilities offer a solution by providing mining companies with the tools they need to enhance the reliability and durability of Continuous Boring Miners.
Investing in ITAMCO’s gear technology is not just an upgrade; it’s a strategic move towards ensuring sustained and efficient potash extraction. The reliability of Continuous Boring Miners equipped with ITAMCO’s precision gears contributes to increased production, reduced maintenance costs, and a positive impact on the bottom line.
A Sustainable Future in Potash Mining
As the potash mining industry evolves, so does the need for innovation. ITAMCO’s advanced gear manufacturing capabilities position it as a driving force in the transformation of Continuous Boring Miners, setting new standards for reliability, durability, and efficiency.
In conclusion, ITAMCO’s commitment to excellence in gear manufacturing extends beyond gears themselves – it’s about empowering the future of potash mining and ensuring a sustainable path forward for this essential industry. As we look towards the future, ITAMCO stands as a beacon of reliability, providing the gears that move us towards a more efficient and sustainable era in potash extraction.
ITAMCO Revolutionizes Gear Manufacturing at THRIVE Energy Conference
The recent THRIVE Energy Conference served as a prime platform for ITAMCO (Indiana Technology and Manufacturing Companies) to unveil its groundbreaking advancements in gear manufacturing technology. Amidst discussions on energy innovation and sustainability, ITAMCO seized the opportunity to showcase its key innovations that are reshaping the landscape of gear production.
At the heart of ITAMCO’s presentation was its cutting-edge use of machine learning and advanced analytics in gear manufacturing processes. By harnessing ML algorithms, ITAMCO has pioneered energy efficient solutions specifically tailored for gear systems. These solutions enable lower energy consumption of the gear manufacturing process.
Moreover, ITAMCO spotlighted its IoT-enabled gear monitoring systems, which provide real-time insights into gear performance and health. Through continuous monitoring and data analytics, organizations can optimize gear operation, prevent unexpected failures, and maximize energy efficiency across various applications.
In addition to its technological advancements, ITAMCO emphasized its commitment to sustainability in gear manufacturing. ITAMCO ensures transparency and traceability in the supply chain, promoting responsible sourcing of materials and ethical manufacturing practices, made in the USA. This not only aligns with the growing demand for sustainable solutions but also reinforces ITAMCO’s dedication to environmental stewardship.
By participating in the THRIVE Energy Conference, ITAMCO demonstrated its leadership in revolutionizing gear manufacturing through innovation and sustainability. Through collaboration with industry peers and stakeholders, ITAMCO continues to drive positive change and shape the future of energy by delivering reliable, efficient, and environmentally conscious gear solutions.
In conclusion, ITAMCO’s participation in the THRIVE Energy Conference underscored its commitment to advancing gear manufacturing technology while promoting sustainability in the energy sector. Through its pioneering innovations, ITAMCO is poised to lead the industry towards a more resilient and sustainable energy future.
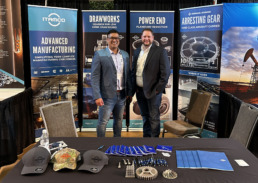
ITAMCO’s Next Generation Gear Manufacturing Revolutionizes Fracking Efficiency in the Oil Industry
In the ever-evolving landscape of industrial technology, efficiency is paramount. Enter ITAMCO (Indiana Technology and Manufacturing Companies), a pioneering entity revolutionizing gear manufacturing with its next-generation capabilities. As the oil industry continues to seek ways to enhance productivity while minimizing environmental impact, ITAMCO’s advancements hold promise, particularly in the realm of fracking.
Fracking, or hydraulic fracturing, has been a game-changer in the oil and gas sector, unlocking previously inaccessible reservoirs and driving production to new heights. However, the process is complex and demanding, requiring precision equipment capable of withstanding extreme conditions. This is where ITAMCO steps in, leveraging cutting-edge technologies to optimize gear manufacturing for fracking applications.
At the heart of ITAMCO’s innovation lies its utilization of advanced materials and processes. By incorporating high-strength alloys and employing state-of-the-art machining techniques, ITAMCO produces gears with unparalleled durability and reliability. This means equipment used in fracking operations can withstand the harsh environments encountered deep within the earth, ensuring uninterrupted performance and extended operational lifespans.
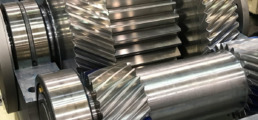
Moreover, ITAMCO’s next-generation gear manufacturing capabilities are characterized by precision engineering and tight tolerances. This precision is crucial in fracking equipment, where even the slightest deviation can lead to inefficiencies or equipment failures. By maintaining strict adherence to specifications, ITAMCO’s gears contribute to smoother operation, reduced downtime, and enhanced overall efficiency in fracking operations.
Additionally, ITAMCO’s commitment to innovation extends beyond traditional manufacturing processes. The company embraces digitalization and Industry 4.0 principles, integrating smart technologies and data analytics into its manufacturing ecosystem. This enables real-time monitoring of equipment performance, predictive maintenance scheduling, and optimization of operational parameters, further enhancing efficiency and reliability in fracking applications.
Furthermore, ITAMCO’s focus on sustainability aligns with the growing emphasis on environmental responsibility within the oil industry. By producing durable, long-lasting gears, the company reduces the need for frequent replacements, minimizing waste and resource consumption. Additionally, the efficiency gains facilitated by ITAMCO’s gear manufacturing capabilities contribute to reducing the overall environmental footprint of fracking operations.
In practical terms, the impact of ITAMCO’s next-generation gear manufacturing capabilities on fracking efficiency is significant. Improved durability and reliability translate to reduced maintenance requirements and lower downtime, leading to increased operational uptime and productivity. Moreover, the precision engineering ensures optimal performance, maximizing the extraction of oil and gas resources from each fracking operation.
Looking ahead, ITAMCO’s ongoing commitment to innovation promises even greater advancements in gear manufacturing for the oil industry. As technology continues to evolve, the company remains at the forefront, driving efficiency, reliability, and sustainability in fracking operations. By embracing the latest technologies and engineering principles, ITAMCO is poised to shape the future of gear manufacturing, transforming the oil industry’s approach to fracking in the process.
In conclusion, ITAMCO’s next-generation gear manufacturing capabilities represent a transformative force in the oil industry, particularly in the context of fracking operations. Through precision engineering, advanced materials, and digitalization, the company delivers gears that enhance efficiency, reliability, and sustainability. As the demand for energy continues to grow, ITAMCO’s innovations offer a promising path towards maximizing the potential of oil and gas resources while minimizing environmental impact.
Joel Neidig Brings Expertise to MTConnect Board of Trustees: A Pioneer in Advancements
In a significant move that underscores the ongoing evolution of manufacturing technology, Joel Neidig, the visionary leader and Director of R&D of ITAMCO, has recently joined the Board of Trustees of MTConnect Institute. This appointment is a testament to Neidig’s remarkable contributions to the field of manufacturing and his commitment to advancing industry standards. Let’s delve into the impressive career of Joel Neidig and the advancements he has spearheaded in the manufacturing sector.
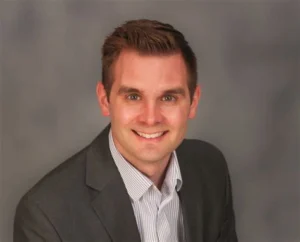
Joel Neidig is a seasoned professional with a proven track record in the manufacturing industry. As the Director of R&D of ITAMCO, a leading provider of precision machining and technology solutions, Neidig has played a pivotal role in driving innovation and implementing cutting-edge technologies. His expertise lies in leveraging digital solutions to enhance manufacturing processes, improve efficiency, and pave the way for the future of the industry.
Throughout his career, Joel Neidig has been at the forefront of advancements in manufacturing technology. One of his notable contributions is the integration of Industry 4.0 principles into ITAMCO’s operations. Neidig understands the importance of embracing digitization, data analytics, and connectivity to create smarter and more agile manufacturing processes.
Under Neidig’s leadership, ITAMCO has successfully implemented the MTConnect standard, a protocol that facilitates machine-to-machine communication and data exchange in the manufacturing environment. This standard plays a crucial role in enabling interoperability between different machines and systems, fostering a more connected and efficient manufacturing ecosystem.
Additionally, Neidig has championed the use of artificial intelligence (AI) and machine learning (ML) in manufacturing. These technologies, when applied strategically, can optimize production processes, predict equipment failures, and enhance overall operational efficiency. Neidig’s forward-thinking approach has positioned ITAMCO as a trailblazer in the application of AI and ML in the manufacturing domain.
Joel Neidig’s appointment to the Board of Trustees of MTConnect Institute further solidifies his commitment to advancing industry standards and promoting collaboration within the manufacturing community. MTConnect, an open standard that fosters connectivity and communication between manufacturing equipment, is crucial for the development of smart manufacturing systems.
As a member of the Board of Trustees, Neidig brings his wealth of experience and insights to contribute to the strategic direction of MTConnect. His involvement is expected to drive the adoption of standards that facilitate seamless data exchange and interoperability across diverse manufacturing environments. This collaborative effort is essential for the continued growth and innovation of the manufacturing sector.
Joel Neidig’s journey from ITAMCO’s CTO to a member of MTConnect’s Board of Trustees is a testament to his unwavering dedication to advancing manufacturing technology. His visionary leadership at ITAMCO has not only propelled the company to new heights but has also influenced the broader manufacturing industry. As a member of the MTConnect Board of Trustees, Neidig will undoubtedly play a pivotal role in shaping the future of manufacturing standards and fostering a more connected and intelligent manufacturing ecosystem.
MxD Welcomes ITAMCO CEO to Board of Directors
December 13, 2023 (CHICAGO) — MxD today announced the addition of Gary L. Neidig, President and CEO of Indiana Technology and Manufacturing Companies (ITAMCO), to its board of directors. ITAMCO is a multi-faceted, advanced manufacturing company with locations in Plymouth and Argos, Indiana. ITAMCO’s core business is in metal machining of precision gears and machined components.
“The perspectives of small and medium-sized manufacturers, which comprise the bulk of U.S. manufacturing, are critical to the conversations MxD leads about driving growth and competitiveness in the sector,” said Berardino Baratta, CEO of MxD. “We’re delighted to welcome Gary Neidig to the board, who brings both leadership in this space and longstanding support of the MxD mission as a former member of our Executive Council.”
Neidig has served in customer service, engineering, and executive management roles during his 42 years in manufacturing while overseeing technology development for advanced manufacturing. He is an active coder and has written engineering and business system applications. Neidig graduated from Bob Jones University with a B.S. in Business Management, and a Minor in Computer Science.
“I’ve always considered MxD to be the premier Manufacturing Institute. Our highest priority should be the opportunity to make tangible improvements in the U.S. manufacturing base through digitalization,” said Neidig. “I am excited to be a part of the MxD board as it helps steer this industry-changing organization, shaping the future of manufacturing in the digital age.”
Neidig will join current board members, Billy Bardin, Global Climate Transition Director, DOW; Katy George, Senior Partner and Chief People Officer, McKinsey & Company; Tony Hemmelgarn, President and CEO, Siemens Digital Industries Software; Mary Isbister, Board Chair and Owner, GenMet Corp.; John Kusnierek, Senior Vice President, LibertyWorks Research and Technology, Rolls-Royce; Shirish Pareek, Chairman & CEO, Adaptec Solutions; Jocelyn Seng, Retired Air Force Major General; Carroll Thomas, Director (Retired), National Institute of Standards and Technology Manufacturing Extension Partnership; and Jay Walsh, Vice President for Economic Development and Innovation, University of Illinois.
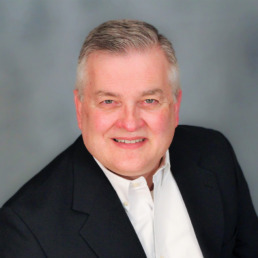
“I am excited to be a part of the MxD board as it helps steer this industry-changing organization, shaping the future of manufacturing in the digital age.”
– Gary L. Neidig, President and CEO of ITAMCO
About MxD
MxD (Manufacturing x Digital) is where innovative manufacturers go to forge their futures. In partnership with the Department of Defense, MxD equips U.S. factories with the digital tools, cybersecurity, and workforce expertise needed to begin building every part better than the last. As a result, our nearly 300 partners increase their productivity, win more business, and strengthen U.S. manufacturing. MxD is also the National Center for Cybersecurity in Manufacturing as designated by DoD.
Media Contact:
Mackie Hill, Marketing and Communications Manager, MxD
mackie.hill@mxdusa.org
312.281.6872
mxdusa.org
ITAMCO's Joel Neidig to speak at the Motion + Power Expo
Save the Date!
Join ITAMCO at the Motion + Power Technology Event this coming Tuesday, October 17th, at 10:30 a.m. for an in-depth discussion on The Future of Gear Manufacturing.
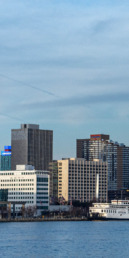
What is the Motion + Power Technology Expo?
Read how ITAMCO Won the Small and Medium-sized Manufacturer of the Year
ITAMCO's Joel Neidig to speak at Fabtech 2023
ITAMCO at Fabtech 2023
We’re thrilled to announce that Joel Neidig will be speaking at Fabtech this year!
Fabtech is North America’s largest metal forming, fabricating, welding, and finishing event. The manufacturing event will feature more than 1,500+ world-class suppliers.
You can find out more about Fabtech here
Join us at the SME Zone in Booth B18000 at 1:00 p.m. to hear Joel discuss the exciting world of Additive Manufacturing!
Want to read more about Additive Manufacturing?
Making CNC Grinding More Energy Efficient
In 2020, the Clean Energy Smart Manufacturing Innovation Institute (CESMII) announced more than $6 million in funding for eight projects to improve energy-intensive manufacturing processes and to strengthen the U.S. manufacturing sector.
ITAMCO, West Virginia University, and Clemson University were chosen to develop hybrid modeling for energy efficient grinding processes for gear manufacturing.
PROBLEM TO BE SOLVED:
Grinding is of the upmost importance in industry, and is essential for creating parts from hard and brittle materials. However, out of all machining processes, it is the one with the highest energy consumption. (SEC) The total grinding time for ITAMCO’s Ring Gear (Pictured below) accumulates 11 hours of energy, and is responsible for 33% of the total manufacturing cost of the gear.
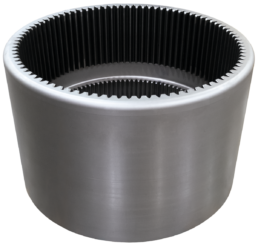
PROJECT OBJECTIVE:
The principal goal is to reduce the extremely high energy consumption of grinding processes for gear manufacturing by at least 15% through hybrid modeling of the grinding system holistically.
TECHNICAL APPROACH:
To achieve this goal, we will develop novel hybrid modeling methods that combine multi-physics equation-based models with data-driven machine learning models. The hybrid model input includes both machine tool parameters and sensor data as well as data from ERP and tool management systems. The hybrid model’s output provides grinding process parameters (wheel speed, depth of cut, infeed duration) as well as grinding tool reconditioning schedule and parameters (dressing and sharpening) that reduce the overall grinding system’s SEC. The model will be prototypically implemented in the industrial testbed will be located on-premise at ITAMCO, a leading US gear manufacturer and SME.
POTENTIAL IMPACT:
The US demand for gears is expected to grow by 6.4% to $40 billion in sales. Grinding will remain the core technology to produce large-scale, high-quality gear components. The novel, scalable, and generalizable hybrid modeling approach and its deployment in the CESMII SM platform environment will provide a blueprint for other use cases to reduce the energy consumption of the US grinding industry.
ITAMCO’s Niles ZP40, which is the primary machine on which their Ring Gear is ground.
BENEFITS TO CESMII:
The project showcases rapid recovery of Smart Manufacturing adoption cost through energy savings and productivity increases in an industry with energy intensive processes. The project creates an opportunity to scale its impact for other interested CESMII members across industries (automotive, aerospace, medical, etc.) and applications (milling, turning, etc.) within the larger CESMII network.
IMPACT VS PERFORMANCE METRICS:
15% reduction in energy consumption & 3-7% increase in productivity lead to an estimated increased throughput of 28 additional units, and annual savings of ~$143,000 and ~1,000t CO2at ITAMCO alone.
Information from Dr. Thorsten Wuest, West Virginia University
ITAMCO Wins Small and Medium-sized Manufacturer of the Year
In an annual event to commemorate innovation in hardtech and manufacturing, ITAMCO has won the small and medium-sized manufacturer of the year award!
From the Fourth Revolution Website: “Founded in 1955, ITAMCO is entering the era of employing the 4th generation and currently employees 124 employees. ITAMCO manufacturers gears that are supplied to the oil and gas industry and is starting to support the EV industry as well.”
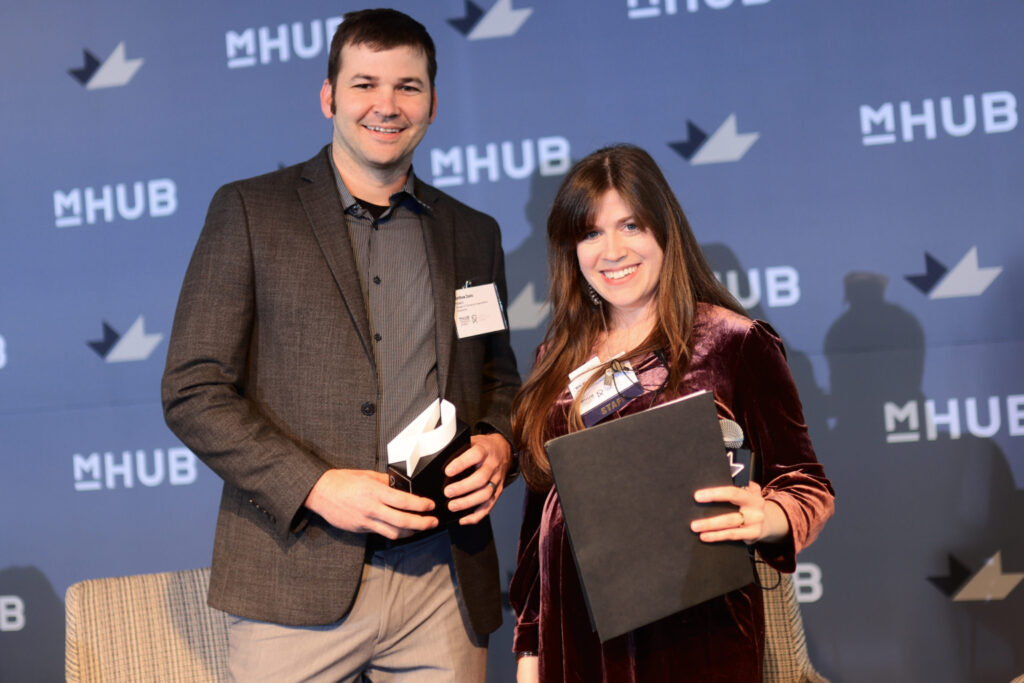
The Fourth Revolution would also go on to congratulate the winners: “Congratulations again to the award winners, and to all the award finalists and nominees. Together, we will ensure that the region’s manufacturing sector is driven, infused with world-class talent, and continues its reign as a global leader into the future.”
For more information, view the original article here.