Connecting with SME
I serve on the SME Member Council and recently wrote an article about the powerful connections SME fosters and growth the organization promotes. Below are my thoughts:
Dear Dianna,
My name is Joel Neidig, and I’m currently serving on the SME Member Council. I’d like to give you a little of my background and what I was doing in 1999. Let me tell you, it wasn’t anything that SME and the manufacturing community as a whole would find significant. I was 16, and on the weekends, my friends and I would game, mostly strategy games like Warcraft (not WoW), Command & Conquer, Age of Empires and, of course, the occasional first-person shooter; Unreal Tournament was our FPS of choice.
In 1999, we didn’t have Wi-Fi (or it wasn’t readily available), and PCs just didn’t seamlessly connect to the internet. We spent most of the time arguing over how the network was going to be set up, yep we were geeks. A bad LAN setup could be the difference between ultimate victory and utter defeat. We had a lot of latency or “lag” back in the day, and we’d try everything we could to improve the experience. (Some of this may sound familiar with what you might be experiencing while at home with all the streaming that’s going on during the COVID-19 crisis.)
But I digress. As teenagers, we had the same issues that manufacturing has: How do I connect to the thing that’s most important to me and get the information I need to succeed? In manufacturing, we’ve gone from Radio Shack TSR80s and single-axis machine tools to Microsoft HoloLens and machine tools that are multiaxis, multitasking and multichannel. Without a standard way to communicate from machine-to-machine, we manufacturers are like me and my friends as teens — we’ve cobbled our devices together to get what we want or settle for less. So what’s a standard way manufacturing engineers can communicate and connect, especially in this time of crisis we’re in? Enter SME.
I first heard about SME in 2013 when a colleague and former international director of the SME board mentioned I should join. He told me it would be a great way to connect to other engineers and young professionals in the manufacturing community, so I joined. About a year and a half later, I was awarded the 2015 Dennis S. Bray Outstanding Young Manufacturing Engineer Award, which was a great honor and also very meaningful. As an added bonus, my SME membership connected me with so many other professionals, not only my age but mentors that I’ve learned a great deal from over the years.
From there, I connected with so many universities and Fortune 500 organizations that really propelled my career to collaborate on so many projects with other like-minded manufacturing professionals. One of my favorite events is SME’s North American Manufacturing Research Conference (NAMRC). I really enjoy hearing all the paper presentations and new research and technology that comes out every year at this event. I also participated and was a finalist in two of the Blue Sky Competitions, which is a lot of fun and a great experience!
Just like the early days of the internet and even today, SME provides a way to connect with manufacturing professionals across the globe, leveraging a knowledge base that I otherwise would not have access to. And even though we’re nestled in our homes for the continuation of the crisis, we have a community we can rely on and be digitally connected to via SME Connect. So check it out, there’s a whole community there for you!
To learn more about your member benefits and encourage others to join, go to sme.org/membership-benefits.
Sincerely,
Joel D. Neidig
CEO and Co-Founder, SIMBA Chain
Director of Research & Development, ITAMCO
SME Member Since 2014
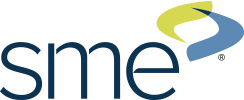
SME helps manufacturers innovate, grow and prosper by promoting manufacturing technology, developing a skilled workforce and connecting the manufacturing industry.