Additive Manufacturing Optimal Orientation and Support Location
During an additive manufacturing (AM) part builds, support structures are essential. They form the basis for the part foundation and providing structural support. They are also critical in eliminating part warp during powder recoating and improving heat extraction generated from the laser sintering.
CHALLENGE
With direct metal laser sintering (DMLS), surface temperature gradients and sintering-induced shrinkage can lead to unanticipated residual stress and part distortion. The goal of this project was to develop a modeling tool that would determine optimal part orientation and support location to minimize the likelihood of distortion during the DMLS process.
Project Partners
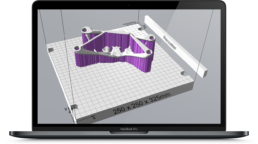
APPROACH
An in-depth survey was conducted to learn as much as possible about how design/manufacturing engineers currently handled these issues. This allowed greater understanding of the rules used to select an optimal part orientation. These rules and insights were then codified to automatically generate an optimal part orientation. Work was also done to develop a support minimization function and create a heat transfer model for DMLS allowing a prediction of thermal mass and temperature gradients to generate a minimal part distortion model.
The research and development was compiled into plug-in for AutoCAD Inventor™ called ATLAS. Subsequently it has been developed into a stand-alone, web-based software.
RESULTS
This work resulted in the introduction of a new type of model for distortion prediction in DMLS printing: a Thermal Circuit Network (TCN) and a Quasistatic Thermomechanical Model (QTM). The model simulates the support-removal process so on-substrate and off-substrate displacement and residual stress can be predicted. The TCN-QTM model was validated against experimental data of disk samples with different dimensions and build orientations, demonstrating a relative error less than 15% in terms of radius of curvature at the top surface of the disks and an agreement in trends of the residual stress. The distorted shapes of a horizontally and vertically built prism predicted by the TCN-QTM model both qualitatively and quantitatively matched the distortion measured by others cited in the literature.
In the case study of simple and complex contoured parts, TCN-QTM was further validated. The TCN-QTM models outperformed novice operators on metrics of maximum distortion, number of attempts, and energy usage. Specifically, maximum distortion was reduced from as high as 0.3 inches to 0.01 inches; the number of attempts to achieve a successful build was reduced from a high of six attempts to a single attempt; and energy usage, as measured by BTU’s per part, was reduced by 86%. The combined TCN-QTM model is faster in comparison to existing DMLS prediction algorithms, providing predictions in as little as ten minutes for simple part geometries.
As a direct result of this project, a new company, Atlas 3D, was established and the ATLAS software has been commercialized as Suntata™, a cloud service, hosted on Amazon Web Services to provide highly scalable computing resources with proven security.
Sunata™ answers the optimal orientation and support structure question for the user. Users simply upload their designs (.STL CAD file) and Sunata™ scientifically models the part in 100 different orientations to arrive at the optimal orientation and associated support structures. In recent months, Atlas 3D has greatly expanded Sunata’s™ capabilities to include build cost estimates, distortion mapping, parts nesting on the build plate, and much more.
Most recently in November 2019, Siemens has announced it has signed an agreement to acquire Atlas 3D. Atlas 3D will join Siemens Digital Industries Software, where its solutions will expand additive manufacturing capabilities in the Xcelerator portfolio of software.
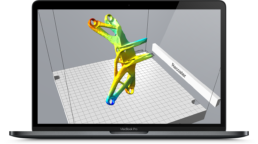